Image 1
Now that technology is evolving so rapidly, embedded vision systems are increasingly used in automotive safety, automation of industry, consumer electronics, and healthcare. From a 2023 start at $16 billion, the global embedded vision market is expected to grow to over $40 billion by 2027, driven by advances in AI, robotics and IoT. Ensuring that the components of a camera are dependable and effective is vital to take advantage of growth, providing your product with robust and stable image results. The following blog considers what makes and breaks a camera hardware design:
1. Image sensor selection is the core of the camera.
Selecting a proper image sensor is key. It sets the camera’s resolution, low-light sensitivity, dynamic range, and power draw. Consider the following:
- Resolution & Frame Rate – More resolution does not always equal better. Match it to the application.
- Shutter Type – Rolling shutter is usual but can create distortion in the case of a moving scene. Global shutter is preferable for quick-moving objects.
- Pixel Size – Bigger pixels collect light, enhancing low-light capabilities.
- Spectral Sensitivity – Certain applications demand detection of infrared or special wavelengths.
CMOS sensors are used in most embedded systems because of their small size, power efficiency, and cost.
2. Lens and Optics: Forming the Visual Output”
Even the greatest sensor can’t produce excellent images if there is not a comparable lens. Your optics determine the image quality, focus, and view angle. Take into consideration:
- Focal Length & Field of View (FoV) – Do you require wide angle to cover a room or telephoto to view far-away objects?
- F-number/aperture – A smaller f-number means greater light entry, ideal for low-light conditions.
- Distortion and Aberration Control – Of paramount importance in medical, security, or vision-AI applications where precision is crucial.
- Autofocus or Fixed Focus – Fixed is quicker and less expensive; autofocus is used in variable-distance scenes.
Optics are carefully aligned and tested against the sensor to exclude artifacts or misfocus.
3. Image Signal Processing (ISP): From Raw to Real
Raw sensor data isn’t pretty—it has to be processed. ISPs deal with:
- Color correction and white balance
- Noise Reduction
- High Dynamic Range (HDR) Merging
- Gamma correction & sharpening
Integrated ISPs are available in some of the sensors. For others, and primarily embedded systems, the SoC’s (e.g., NXP, Ambrella, TI, Qualcomm chipsets) or a separate ISP chip does the processing. The proper ISP strategy is vital to image quality and not overwhelming your system.
Image 2
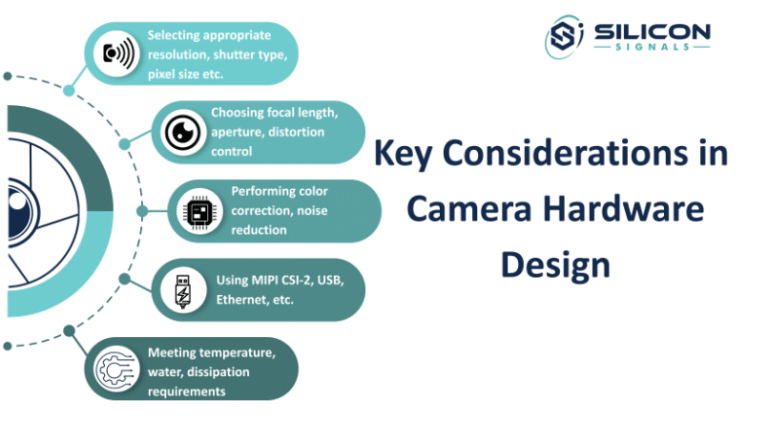
Bring your camera-based products to life with expert hardware design solutions!
From image sensors to lens selection—we help you get it right from the start.
4. Connectivity & Interface: Delivering the Data”
Based on your system requirements and processing platform, you will find that you must select the appropriate interface:
- MIPI CSI-2 – High speed, power-saving, suitable for embedded applications.
- USB 3.0/3.1 – Plug-and-play application for prototyping or PC-based systems.
- LVDS / GMSL – Low-latency, long-distance automotive system transmission.
- Ethernet/IP Streaming – For network-based surveillance or remote monitoring systems.
Ensure that the bandwidth supports your resolution and frame rate without bottlenecks.
5. Mechanical Design and Form Factor: Fit is Critical
Numerous products require tiny, embedded camera modules. The key factors are:
- Size and Form – Particularly for wearables, drones, and small IoT devices.
- Mounting & Vibration Resistance – Automotive or industrial cameras have to resist vibration.
- Heat Dissipation – High-performance processors or sensors produce heat—it is crucial to dissipate the heat to avert degradation.
6. Environmental Tolerance & Compliance
Cameras frequently have to function in extreme conditions. Your design must accommodate:
- Operating Temperature Range
- IP Rating – Protection against water and dust in outdoor/industrial applications.
- Shock & Vibration Standards
- Regulatory compliance – FCC, CE, RoHS, STQC and NDAA etc., based on your market.
If not suitably protected and certified, your camera will underperform or even fail in the field.
Conclusion: Getting Camera Design Right from the Start
Camera hardware design combines the intricacies of electronics, optics, and system engineering. The design choices affect not only image quality, but also the performance of the device, power consumption, manufacturability, and the overall user experience.
At SiliconSignals, we have expertise in designing entire camera systems from end to end—from sensor choice and lens integration to ISP tuning and optimization of embedded platforms. From designing a vision-enabling industrial solution, medical system, or smart consumer product, our skills guarantee that your camera gets the results where they’re needed.